Equipment
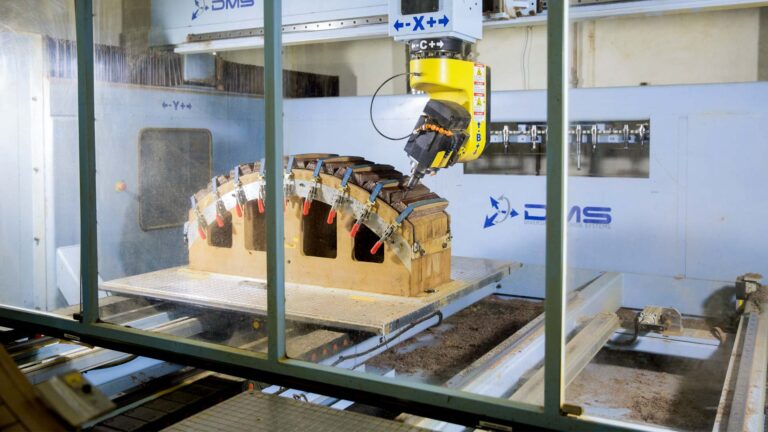
State of the art Equipment
MachineTek produces honeycomb and foam core components using a wide selection of equipment, ranging from fully-automated to hand cutting.
Complex or high-volume core component fabrication utilizes state-of-the-art 5-axis CNC profiling routers. Our 5-axis routers have twin 5-foot square tables which can be utilized separately for greater efficiency or together to accommodate parts up to 5×10 feet.
Less complex parts and bonded panels are fabricated on 3-axis mills and non-CNC equipment such as band saws and custom routers. Semi-automated and template-based processes are used when cost-effective for our clients.
Honeycomb expansion equipment allows aluminum honeycomb to be profiled in the unexpanded form and then expanded, a very cost-effective option when appropriate.
A large automated roll-forming machine allows aluminum honeycomb to be formed into a curved shape, useful for engine nacelle and rocket body component fabrication.
An automated walk-in oven with vacuum and thermocouple capabilities allows for processes such as heat forming, potting, edge bonding, and core drying.
Once fabrication is complete, complex components are verified to be accurate with the use of a portable coordinate measuring machine.