Relieve Pain Points in Honeycomb and Foam Fabrication: Improve Efficiency and Quality
As the aerospace sector experiences growth, increased demand for composite structures incorporating honeycomb and foam core has created pain points for composite manufacturers. While honeycomb and foam core fabrication may initially appear simple, the reality is this unique process requires specialized tooling, fixtures, machinery, programming, and less than conventional manufacturing methods.
Is it prudent to tackle a new or unknown fabrication technique when there are options to safely outsource this process?
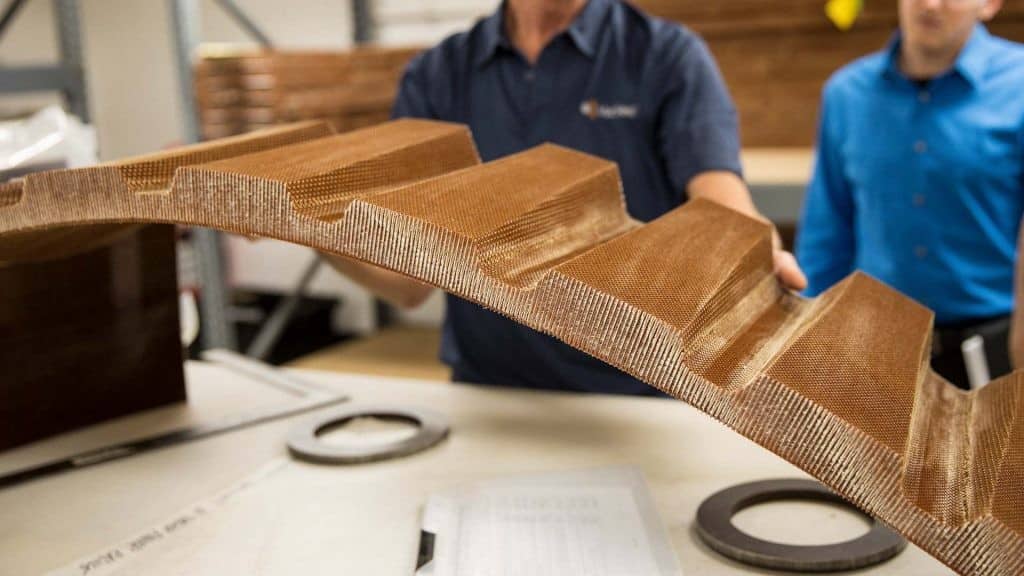
Outsourcing fabrication has many benefits, especially for a composite manufacturer onboarding a new program. The most obvious is capacity. Ramping up a new program places demands on internal resources. While most composite fabrication processes cannot be outsourced, precision honeycomb and foam fabrication accomplished by a trusted and capable outside vendor is a candidate for outsourcing.
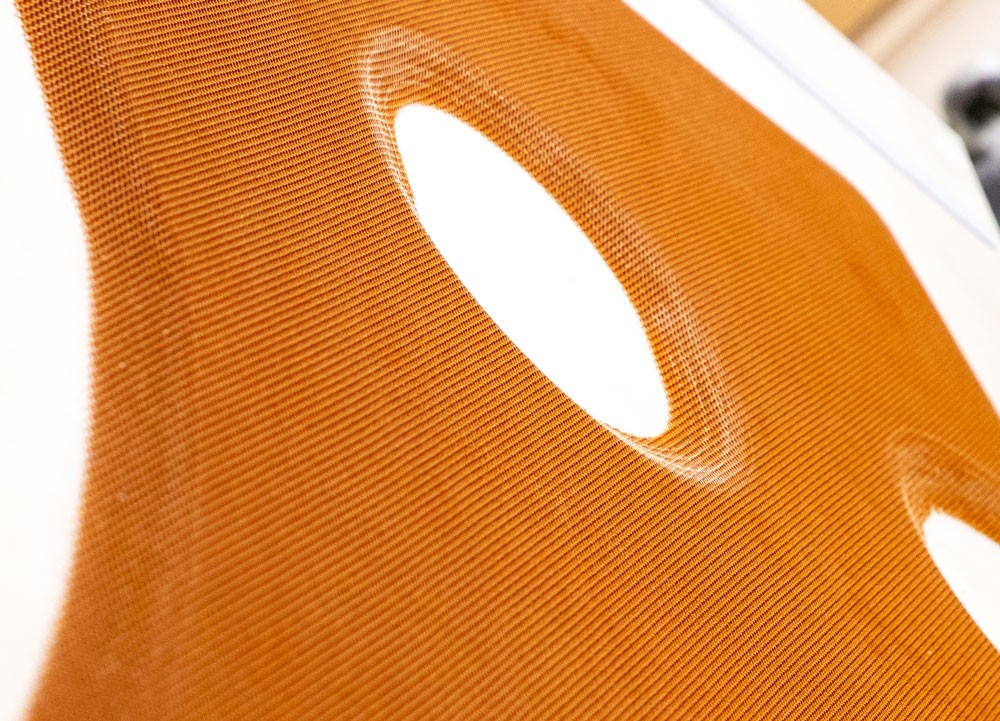
Composite manufacturers also save time by shifting all aspects of fabrication to an outside vendor. Material, often procured by the outside vendor, is fabricated, inspected, and delivered ready for inclusion directly into the layup process. Importantly, fabricated core component characteristics can be verified by the user’s inspection team before being released into the production workflow. A purchasing agent can issue a single order, then simply wait for finished parts to arrive on the production floor.
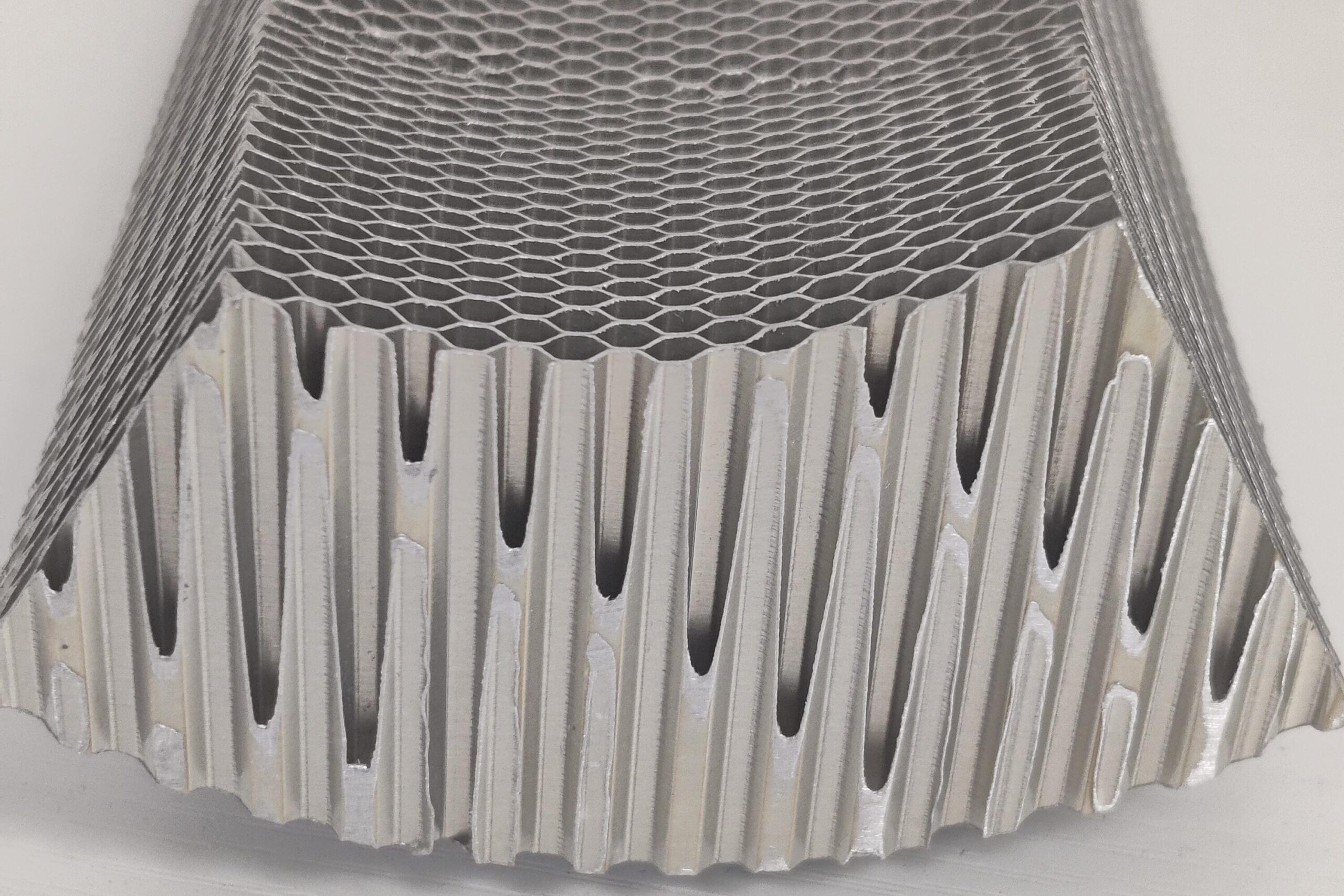
Another benefit of outsourcing honeycomb core fabrication is the precision to be realized from fabrication by an outside vendor specializing in such work. Machining and other processes relating to core component fabrication may appear straightforward, but the knowledge and equipment required to properly and accurately fabricate honeycomb details are very specialized. Machining honeycomb is vastly different than machining solids!
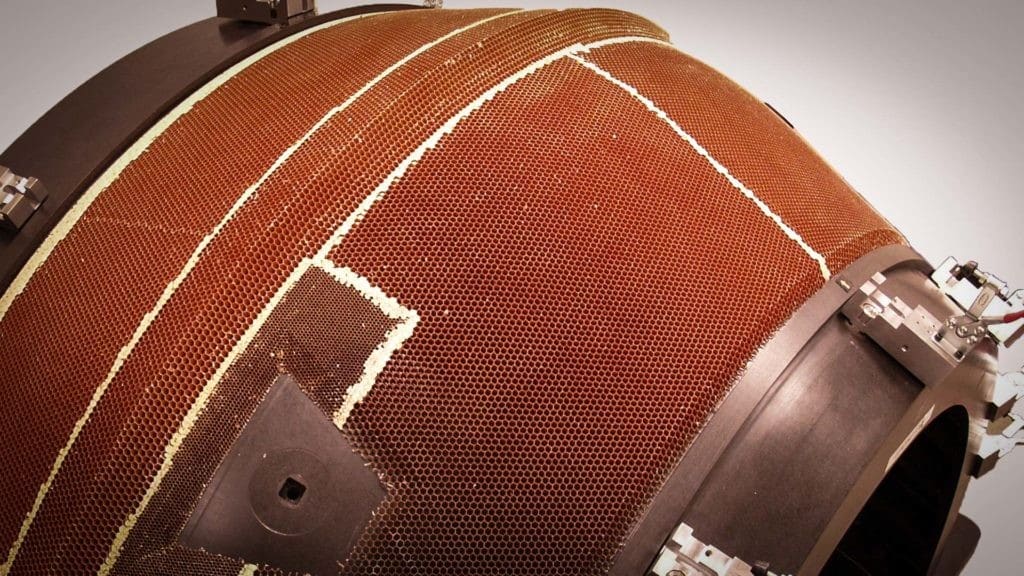
Of course, honeycomb core component fabrication often involves much more than precision machining. Heat forming, edge splicing, potting, film stabilizing, and other advanced processes are often beyond the capabilities of composite manufacturers. Vacuum bagging, oven cycles, shelf-life limited materials, and other aspects of these advanced fabrication processes are often best left to experts in their application.
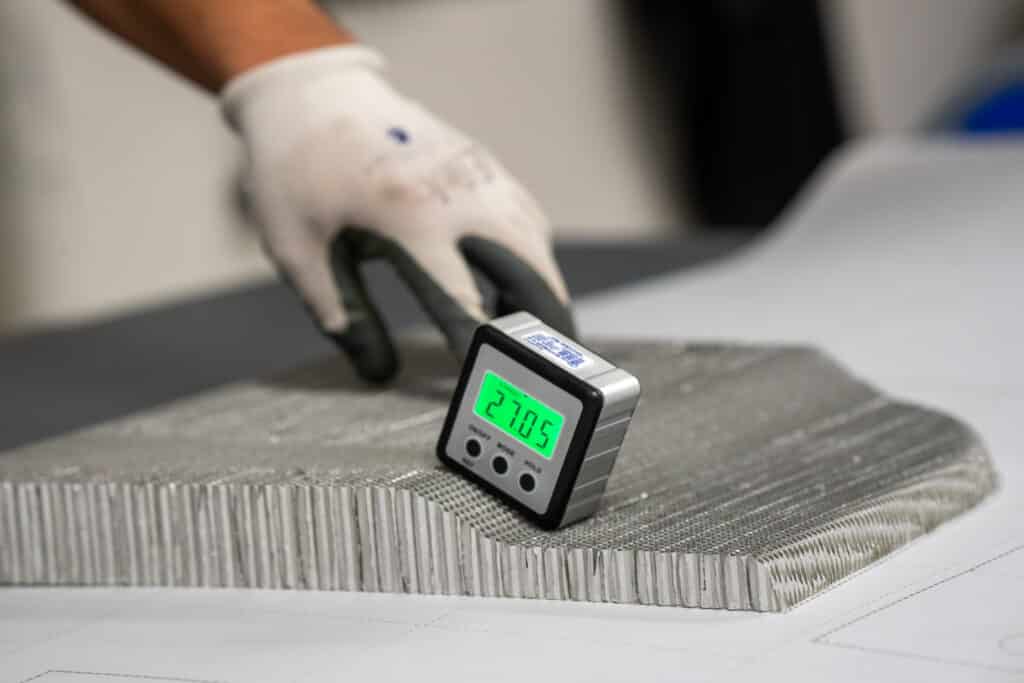
Fortunately, composite manufacturers have the option to outsource the complex, demanding, and time-consuming work of precision honeycomb fabrication to capable outside vendors such as MachineTek LLC in Carlsbad, California. For the past thirty years, MachineTek has specialized in the full range of precision structural honeycomb and foam fabrication for demanding composite manufacturers throughout the U.S. aerospace industry. As these customers have discovered, a trusted partner such as MachineTek can fulfill their fabrication requirements, freeing them to focus on their core competencies.
Top 6 Reasons to Partner with MachineTek for Honeycomb Fabrication
1. Quality – MachineTek maintains ISO/AS9001, NADCAP, and ITAR certifications, and has been qualified by numerous prime contractors for various aspects of honeycomb and foam core fabrication. Consistent, documented, and repeatable processes ensure finished parts comply with stringent quality standards. Perhaps equally important, providing accurate and customized documentation with each shipment allows parts to move seamlessly through the customer’s quality department and onto the production floor.
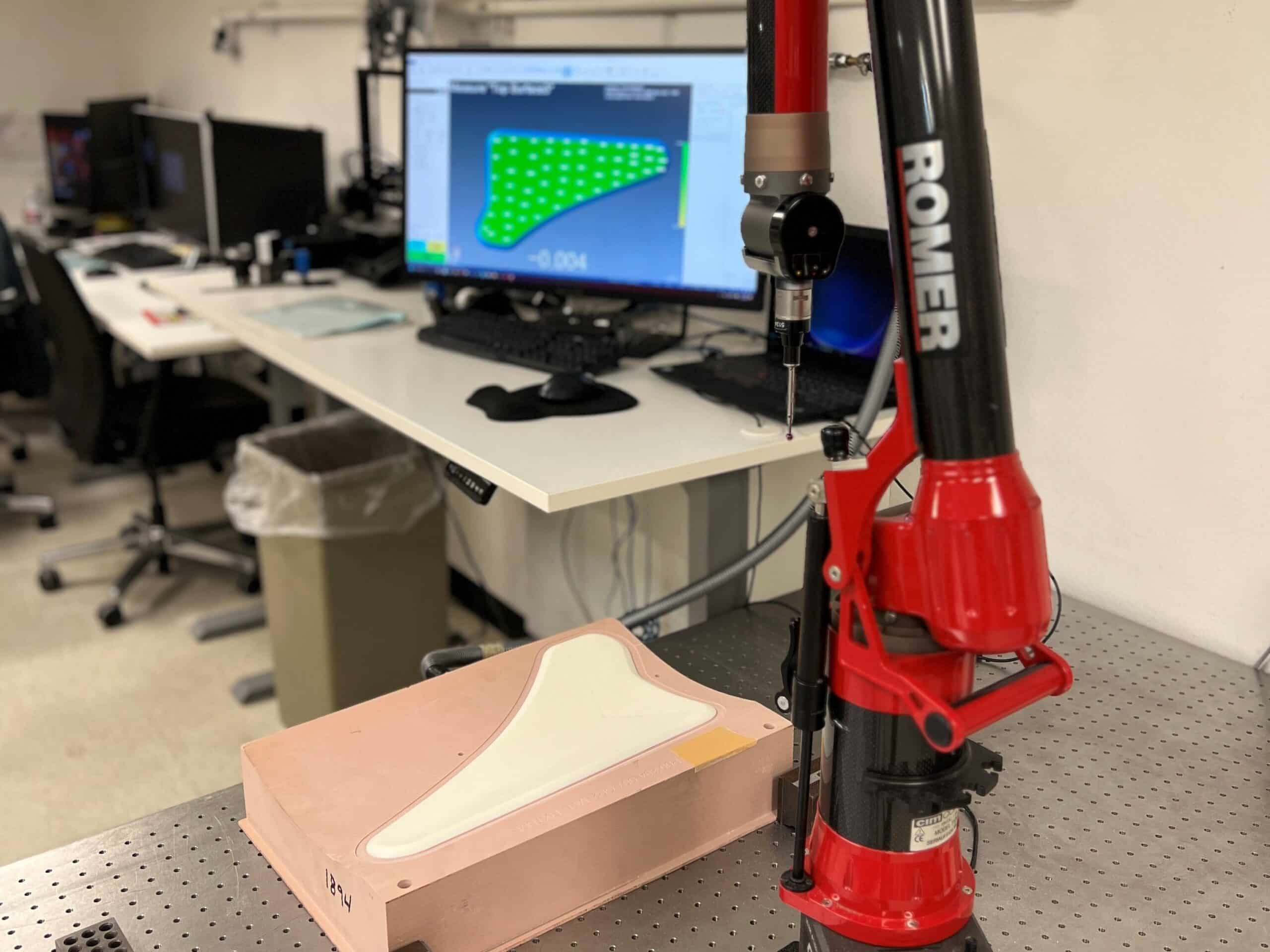
2. Focus – MachineTek specializes in servicing customers’ requirements for high-quality components, delivered on time and at a reasonable price. Once customers experience this combination of quality and value, they realize outsourcing fabrication is a viable and desirable option to free up their time and internal resources.
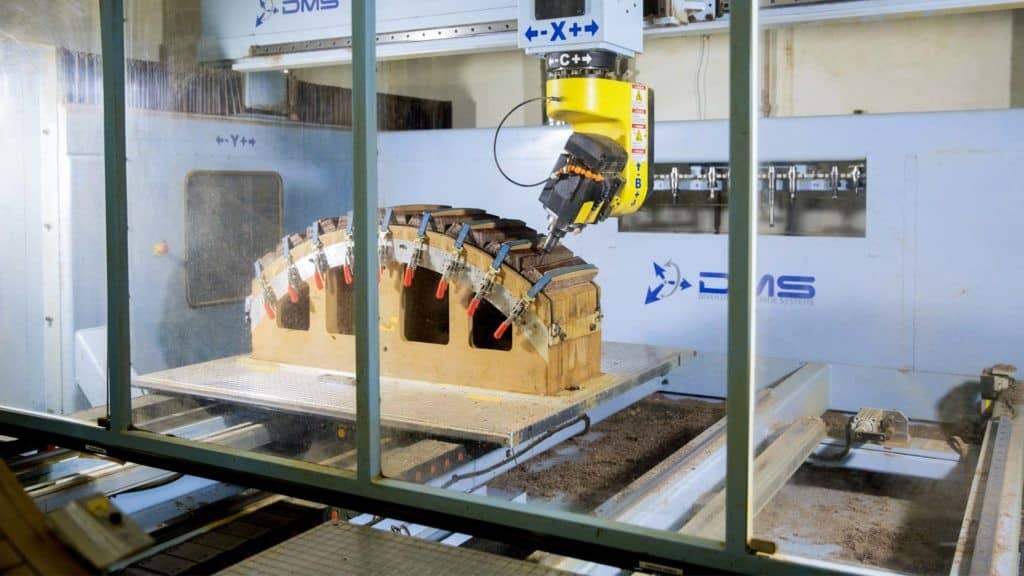
3. Honeycomb and Foam Expertise – It is a common pitfall in fabrication to initially approach part fabrication with manufacturing experience derived from billet machining. The gap in honeycomb and foam manufacturing knowledge is often realized only after the start of internal fabrication, causing sudden and unexpected delays in time-sensitive programs. CNC tool paths, cutting tools, fixturing, and other honeycomb fabrications variables require a unique approach. Relying on the knowledge and experience of the right contract manufacturer can add substantial value to a program. MachineTek’s industry knowledge spans 30 years, supporting hundreds of challenging fabrication programs for a wide range of customers.
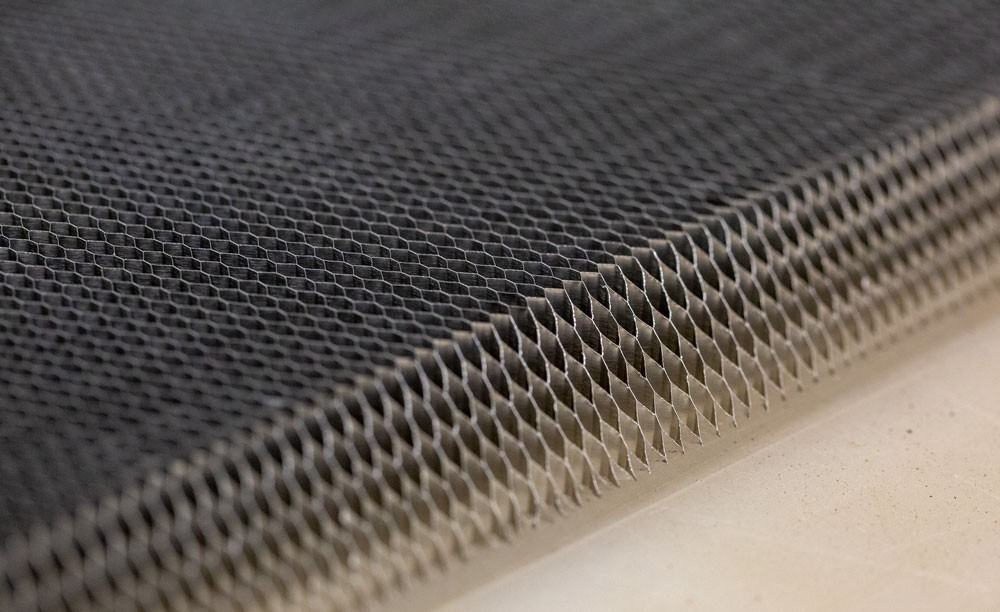
4. Technical Assistance – MachineTek’s engineers provide valuable insight and suggestions to streamline part fabrication and reduce costs. Solid model manipulation and creation, generation of inspection Mylars, design of production and inspection tooling, and other valuable contributions can take the load off resource-constrained customers.
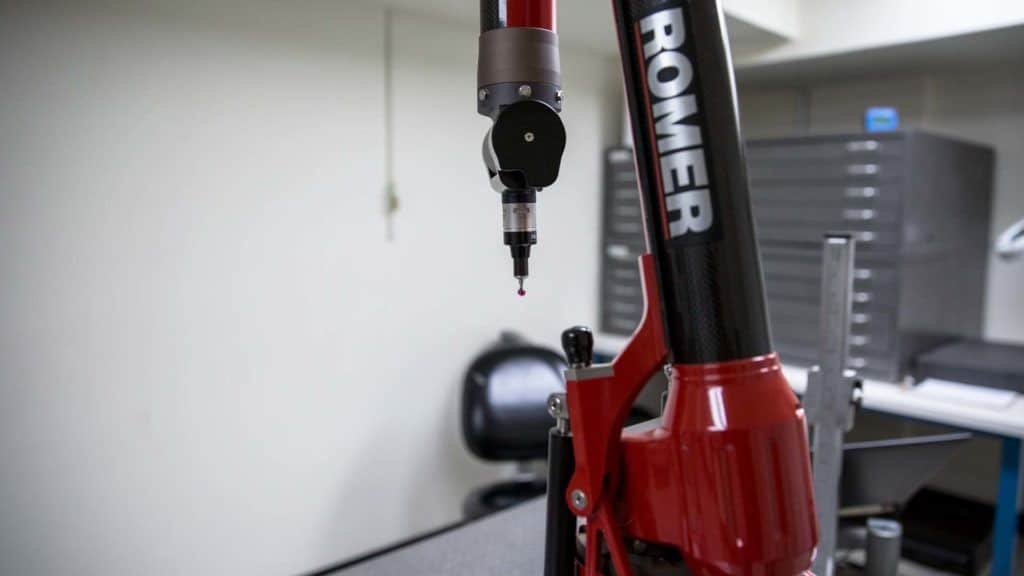
5. Cost Control – Outsourcing secures material and labor at a fixed price. Additional costs associated with internal fabrication such as overhead, utilities, equipment maintenance, tooling degradation, scrap rate, custom fixtures, and inventory costs are eliminated. And, of course, internal management of part production carries its own burdens.
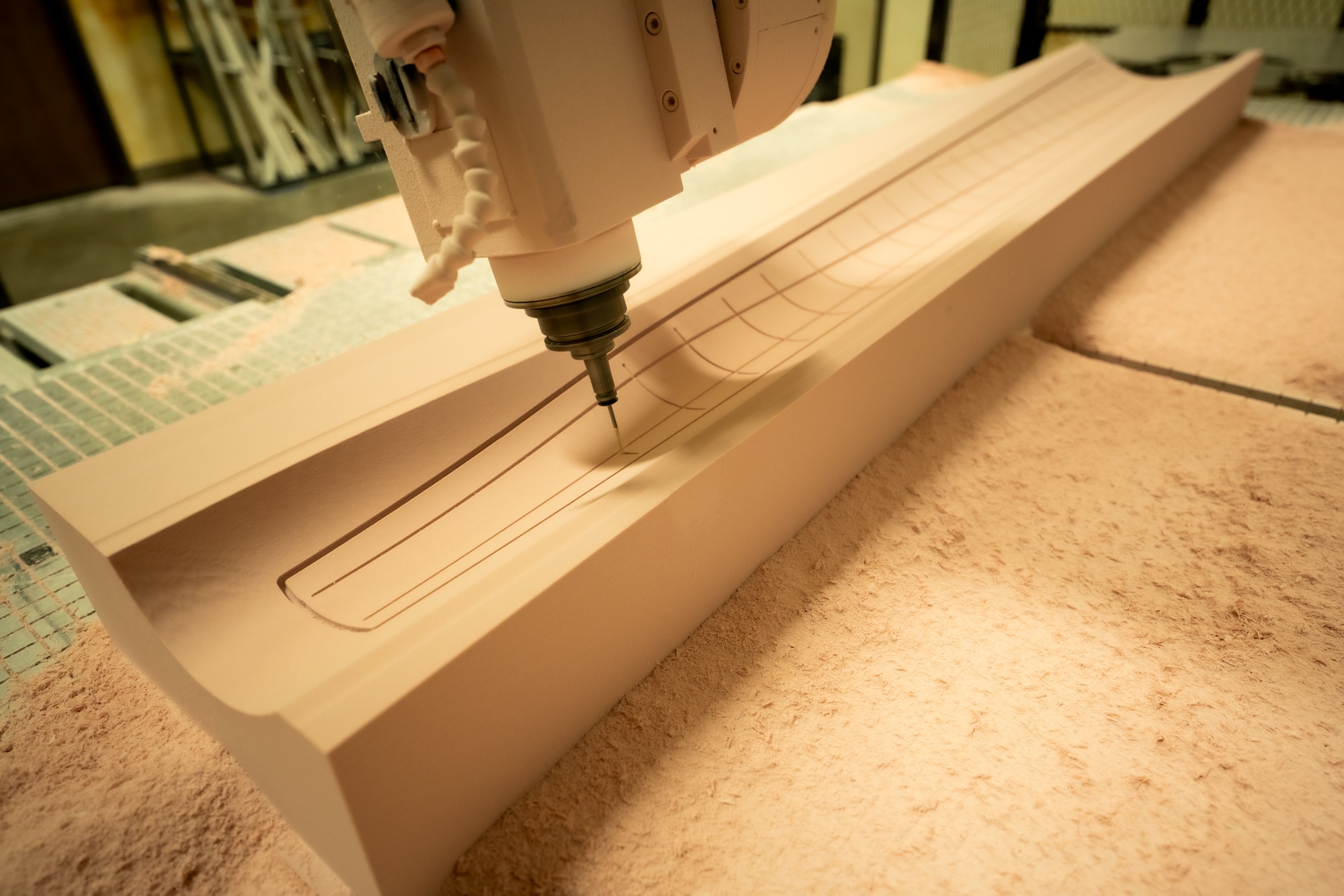
6. Customer Service – With a reputation for outstanding customer service and quick response, customers have come to rely upon MachineTek to solve their honeycomb core sourcing challenges.
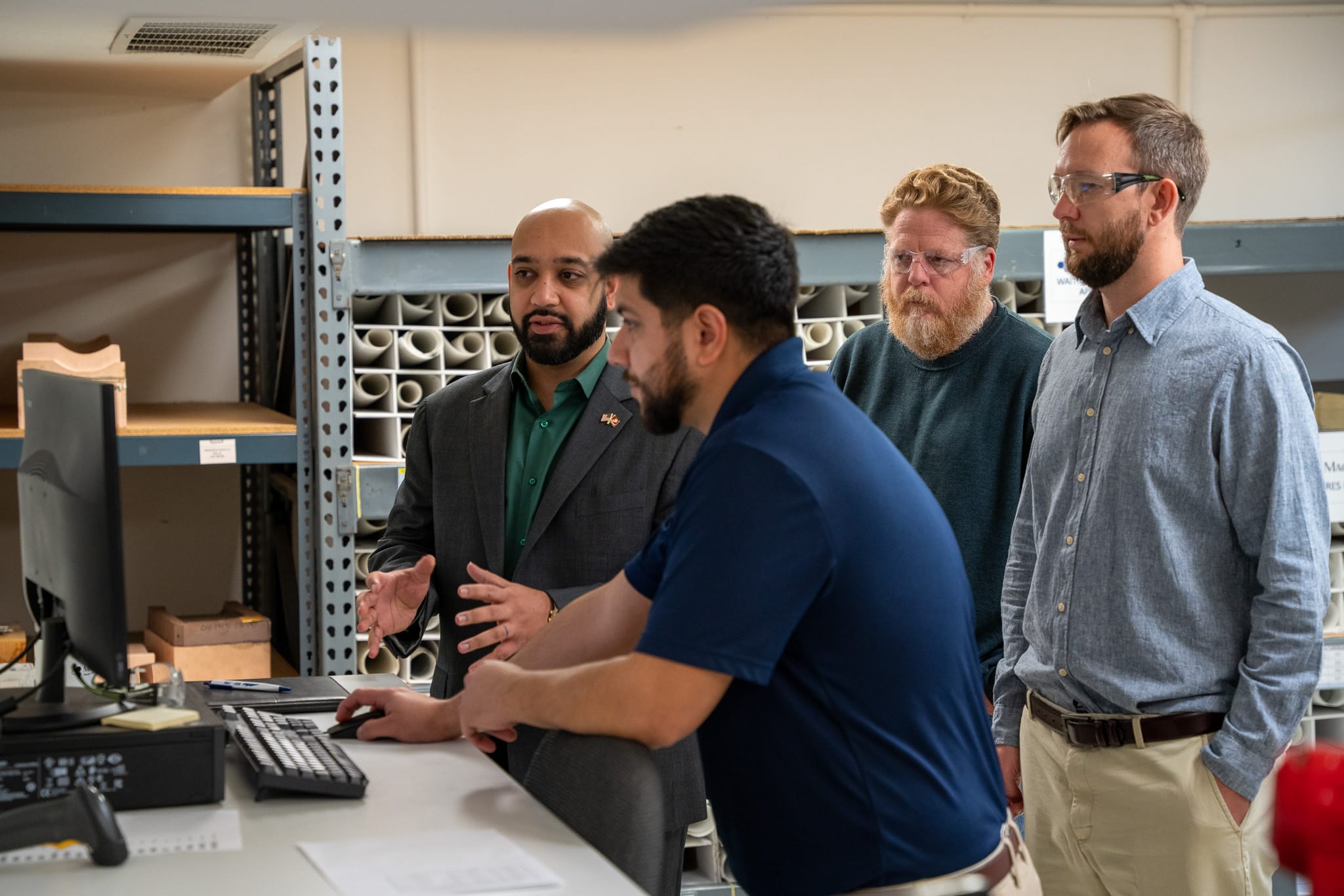
As we’ve seen, by outsourcing honeycomb and foam manufacturing to a trusted vendor, a composite fabricator can utilize its internal resources on its core capabilities instead of struggling with the many challenges of component fabrication.
When an opportunity arises to improve quality, increase profitability, limit risk, and reduce demands upon internal resources, astute composite fabricators turn to the experts at MachineTek for their precision honeycomb and foam fabrication requirements.
760-438-6644
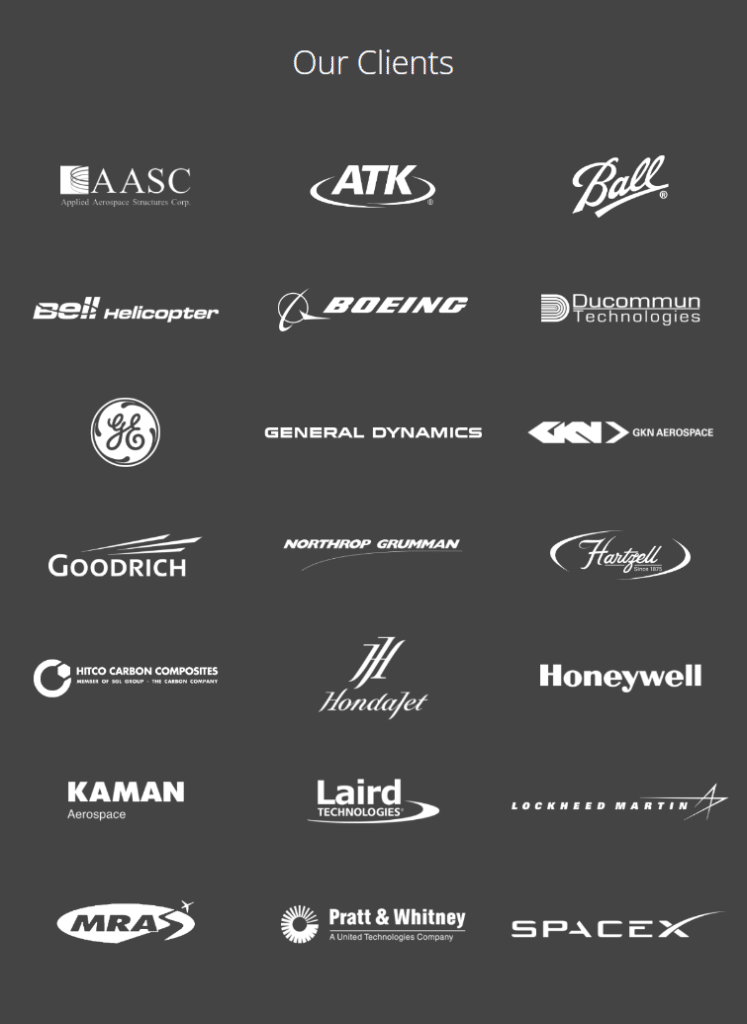